MANHATTAN WEST DEVELOPMENT PLATFORM
New York, USA
Placing a 10.200 sqm segmental post tensioned deck over live railway track
A special custom-built equipment has been used to create a large plaza above the rail metro lines in Manhattan.
To close the gap in the middle of downtown New York Gruppo de Eccher developed an innovative solution to precast, transport and launch the plaza deck.
Before becoming equipment suppliers, we were contractors: this background allows us to find the right solutions to solve problems in the most efficient and safest manner.
Execution
The solutions
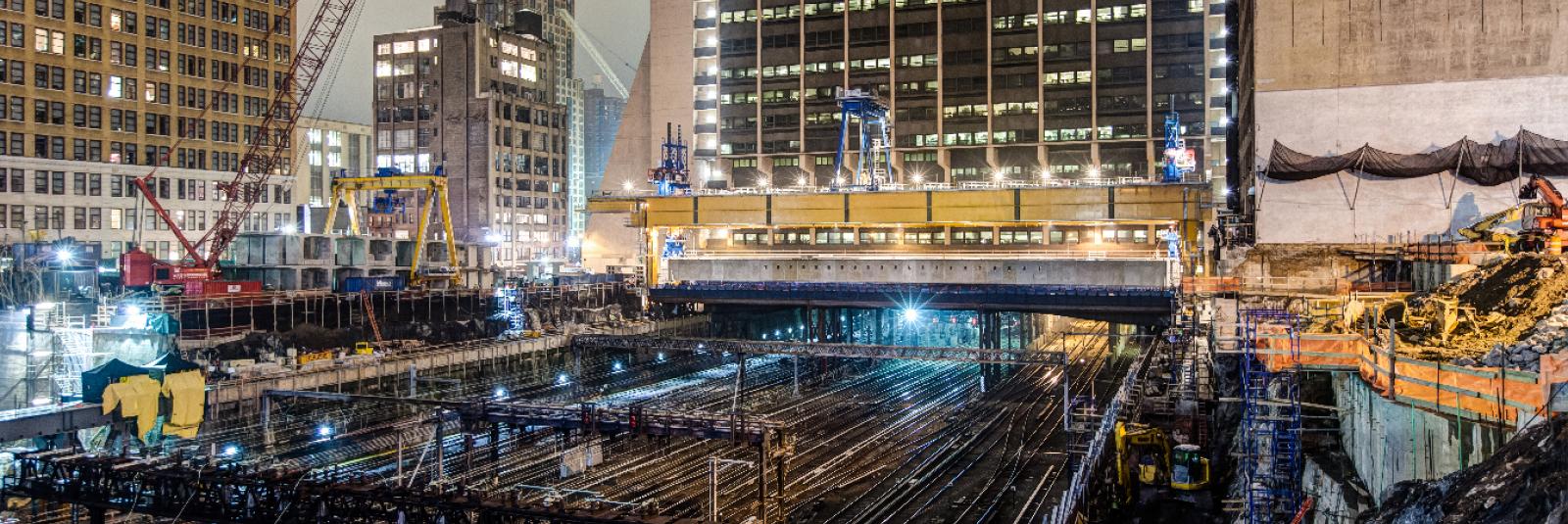
Rail lines and their electrified power systems under the construction yard represented a huge problem for the safety of metro passengers and workers at the site.
The solution came from observing the bridge construction industry, taking advantage from the well known technology of the span by span construction.
2400 precast segmental beams forming 16 parallel decks has been used to cover a 73x146m gap.
Request information
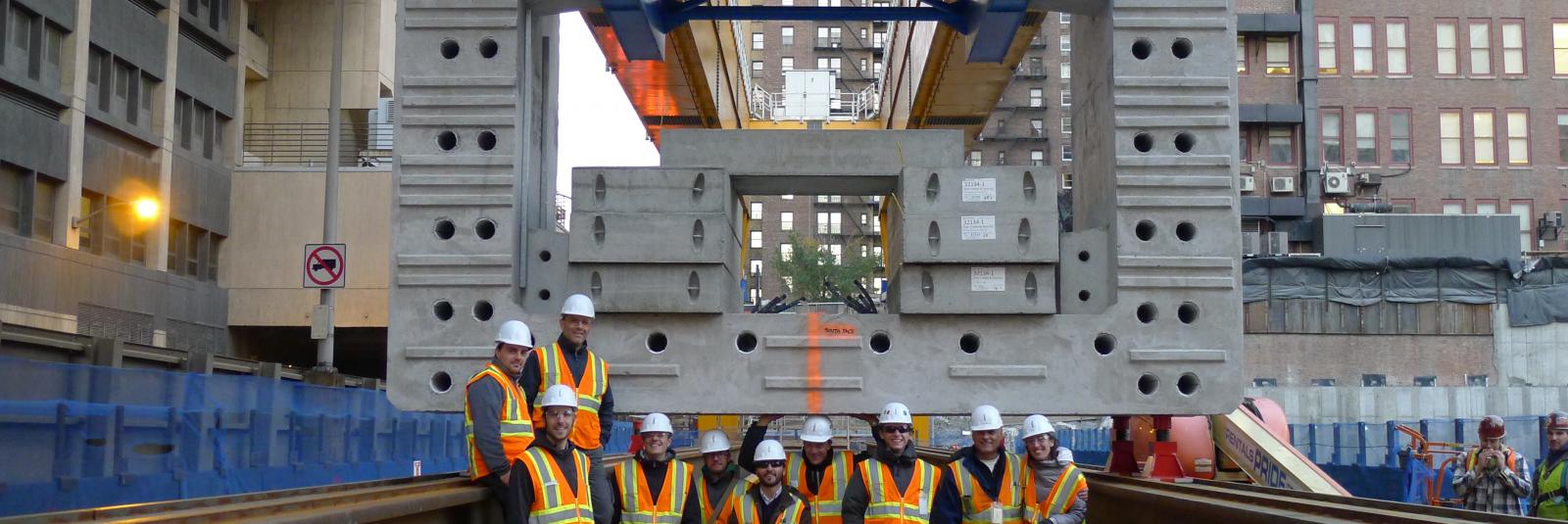
The precast activities were carried out in New Jersey, where labour rates are significantly cheaper than Manhattan.
To allow a safe and efficient transportation of the segment from the precast yard to the site, we designed beams made by several segments each (from 37 to 39). In this way, we limited the size of each segment to 56 t and the typical lenght to 1,93 m.
Request informationPrecasting was an essential part of the project: cycle efficiency for the segment prefabrication was maximised by the supply of three short-line moulds for typical segments, one mould for pier segments and an adjustable mould able to cast segments with a a variable web thickness. A straddle carrier serviced the staging area in Manhattan off-loading the segments that were brought in and placing them in their temporary storage location.
The whole operation was designed to minimise the time needed for PT bar tensioning and for the completion of the connections. Each beam required 100 t of post tensioning supplied by TENSA. We used 20 tendons with 37 strands and 14 with 31 strands for each span. Due to the important permanent design loads (new buildings has been constructed over the plaza) PT ratio - the weight of the steel PT strand per square metre of deck area - was three times higher than for standard bridge construction applications.
The special equipment supplied by DEAL have been able to erect 16 adjacent beams, each with a lenght of 73 m each. The assembly process for the deck was very similar to that of a sequential span-by-span bridge. The key difference was that a single platform was being built so there was no need for a gantry that could launch segments from pier to pier. Instead, the equipment moved sideways to place one complete bridge span adjacent to the next.