Gran Manglar Viaduct
Cartagena de Indias, Colombia
A viaduct built through a nature reserve with the innovative top-down method
The Gran Manglar Viaduct is part of the project for the construction of the Cartagena de Indias e Barranquilla highway. The viaduct is 3.7 km long and crosses the Cienaga de Tesca lagoon. For the construction of the viaduct a top-down construction method has been chosen. All structural elements, including piles, pile-caps and beams, are made of precast concrete and are erected using a special erection equipment designed for this type of construction which does not require access from the ground.
Colombia's longest bridge, which will pass over the La Virgen swamp at Cartagena, will be ready in June 2018, four months ahead of the original schedule
Execution
The solutions
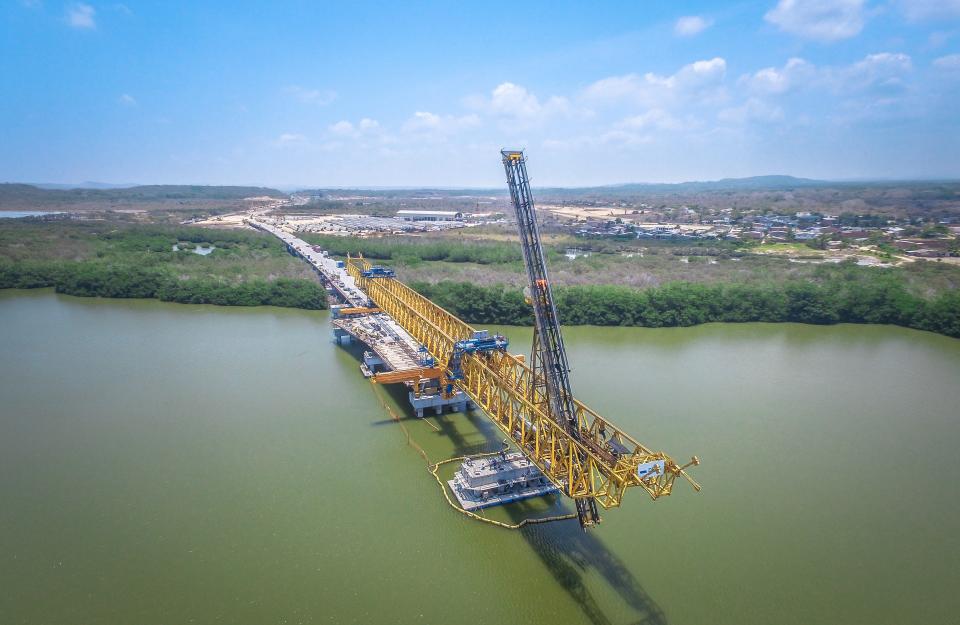
The top-down construction method avoids the need for dredging, concrete slabs and the construction of access roads, which otherwise would have damaged the natural reserve for years.
The solution consists of a launching girder which is able to drive piles in the marshland and to launch pile caps and girders.
Request information
The viaduct consists of 129, 37m-long spans and it is entirely made up of prefabricated, prestressed concrete elements, excluding the completion elements and the cast-in-situ slabs.
Prefabrication of the elements takes place in a precast yard adjacent to the abutment 130. The implant consists of three production lines: pile caps, piles and girders.
Request informationAn alternative construction method has been implemented starting from the original proposal envisaged by Colombia's National Infrastructure Agency, and resolves all the projects requirements and issues.
A similar project has already been developed by Deal on the Washington Bypass, North Carolina.
The implant consists of three production lines:
• Pile caps: consisting of a "long line" mould for production of match cast elements.
• Pile: moulds are modular for the production of piles of different lengths (30-58 m). Each mould is equipped with a fixed bulkhead used for the installation of mechanical connection devices between the pile elements.
• Girders: made from a mould for the production of beams;
The movement of the prefabricated elements is carried out by means of the gantry crane and the straddle carriers equipped for the different elements.
On typical spans, the gantry drives six piles and then sets the precast concrete caps in three pieces on the piles. The caps are post-tensioned and infill concrete is placed. The concrete infill is loaded into buckets and transported to the leading end of the truss using the gantry trolley. The trolley maneuvers the bucket into the position required for concrete placement. Next, three beams are placed by the gantry and the concrete deck is cast. Once the 28 MPa concrete compressive strength is achieved, the gantry moves forward, and the cycle is repeated for the next span